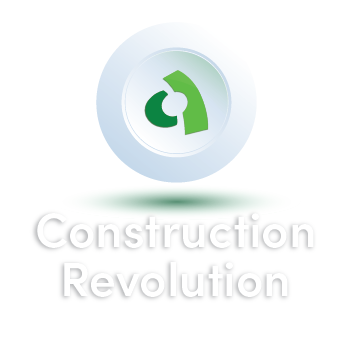
Episode 52 |
November 14, 2024
Advancements in Low-Carbon Construction Technologies
In This Episode
Join us for an engaging and insightful panel discussion from 2024 Net Zero Construction Conference, hosted by Aali Alizadeh, Ph.D., Co-Founder and CTO of Giatec and Technology Chair of The Net Zero Construction Conference. This episode dives into groundbreaking advancements in low-carbon construction technologies, highlighting both the promising opportunities and the significant challenges involved in their industry adoption.
Our distinguished panel of experts features: Professor Jason Weiss from Oregon State University, Heather Brown, Ph.D., Vice President of Quality Control/Quality Assurance at Irving Materials Inc. (IMI), Donn Thompson, Senior Director of Building Innovations at the National Ready Mixed Concrete Association (NRMCA), Brandon Williams, Business Development Manager at Sublime Systems, Lisa Barnard, Sustainability & EPD Program Manager at Chryso Saint-Gobain, and Pouria Ghods, Ph.D., Co-Founder and CEO of Giatec. Together, they offer a wealth of knowledge on the latest advancements in sustainable construction, sharing how innovative materials and solutions are transforming the industry.
Don’t miss this opportunity to learn from industry leaders as they share actionable insights and strategies that can drive meaningful change in the construction landscape.
Want to dive deeper into conversations like the ones in this episode? Join us at the Net Zero Construction Conference 2025 on March 19-20 in the Virbela Metaverse! Experience two days of expert panels, innovative insights, and networking opportunities focused on low-carbon construction technologies. Learn more and get your tickets on the N0CC website!
Host
Aali Alizadeh, Ph.D.
Co-Founder & CTO, Giatec Scientific Inc.
Guests
Donn C. Thompson, AIA, LEED AP BD+C
Senior Director, Building Innovations, NRMCA
Pouria Ghods, Ph.D
Co-Founder and CEO, Giatec Scientific Inc.
Brandon Williams
Business Development Manager, Sublime Systems
Heather J. Brown, Ph.D.
VP, Quality Control/Quality Assurance, IMI
Dr. Jason Weiss
Professor, Oregon State University
Lisa Barnard, LEED AP, WELL AP
Sustainability & EPD Program Manager, Chryso & GCP; Saint-Gobain Construction Chemicals
Podcast Transcript
Aali Alizadeh:
Welcome, everyone. I’m Aali Alizadeh, Giatec’s Co-Founder and CTO, as well as the Net Zero Construction Conference Technology Chair. Really excited to host today’s panel. The title of the panel is Advanced and Low Carbon Construction Technologies. We’re going to focus on opportunities and challenges for industry adoption for these low carbon materials, solutions and innovations. And I’m really looking forward to insightful conversations with the brilliant innovators we’ve gathered today. If you have any questions during today’s panel discussion, please feel free to share that in the chat area. The panelists might be able to add just those questions during the session, but also at the end we’ll have an opportunity to have a Q&A.
Before we start today’s panel, I would like to share some of the discussion points from last year’s panel. The title for that panel was Building for Green Future, and we discussed how important sustainability is on the job site and what are the main advantages and challenges of that when we look at the practical aspects of it. And what factors were influencing sustainable change and what trends we were seeing in that area emerging. And how the construction industry could start to better use technology to be more sustainable. Today we’ll be digging further into the last point, with topics that we put together for this panel to understand the opportunities and challenges for our industry in adopting the advancements in low carbon technologies.
So let’s kick it off now, and I thought a good place to start would be to find out more about our panelists with diverse backgrounds from academia to different industries and organizations. And this would allow our audience to have some context as we dive into the panel. And I think we’ll start with your name and few sentences describing your career and area of expertise, that would be great. So let’s just start with Jason, please.
Jason Weiss:
Jason Weiss from Oregon State University. I’ve spent most of my career working on value added products, whether it’s shrinkage reducing admixtures, internal curing, performance specs. So right now, a big, big movement toward low carbon concretes.
Aali Alizadeh:
Awesome, thank you and welcome to this panel. Heather.
Heather Brown:
Heather Brown. I’m currently with Irving Materials Incorporated, better known as IMI, is a ready mix producer corporate out of Indianapolis. We cover several Midwestern and southern states. In my previous career I was a 20-year college professor teaching solely in concrete construction, so very steeped in academics and in research as well, and enjoy being on the industry side of life.
Aali Alizadeh:
Thank you very much for joining us again today. And let’s go to Don, please.
Donn Thompson:
Hi, Donn Thompson, I’m Senior Director Building Innovations for the National Ready Mixed Concrete Association. Based in the Chicago market, I cover eight states supporting our Build with Strength program, which is a program designed to spell the myths about the use of ready-mixed concrete in the building environment. I have about 25 years experience in the concrete industry, and prior to that I worked for about 20 years as a licensed architect in the Chicago area. And I’m glad to be here today.
Aali Alizadeh:
Awesome. Brandon, please.
Brandon Williams:
Brandon Williams, Product Success Manager with Sublime Systems. My role with Sublime is to interface with the industry and to make sure that our technology is a form-fit-function replacement. So, 10 years experience in the ready-mixed and concrete industry. I’ve worked as a lab technician, lab supervisor, project manager, plant manager, and a senior project engineer. So, I’m excited to participate in the panel today.
Aali Alizadeh:
Welcome to the panel, Brandon. And Lisa, please.
Lisa Barnard:
Hi, Lisa Barnard. I’m the sustainability and the EPD Program Manager for North America with Chryso GCP, part of Saint-Gobain. I’ve been in the construction chemicals world for close to 15 years now, working a wide vast portfolio of products, working with architects, engineers, owners, developers, on specification development projects, and now focused on the concrete industry and working with our customers.
Aali Alizadeh:
Last but not least, Pouria, please.
Pouria Ghods:
Morning everyone, Pouria Ghods, Co-Founder and CEO at Giatec. Yeah, I’ve been working in concrete materials over the past 20 years, both on the research side and now it’s more on the industrial application. We are glad to be here today.
Aali Alizadeh:
So, let’s start with our first topic. In the past few years, we have seen many new research and development projects in the field of low-carbon construction materials and technologies. In practice however, construction technology implementation is still behind. There’s that gap, that lag that we need to add. So let’s look at some of these technologies and discuss how they can influence the industry directions moving forward.
So let’s start with Jason. Back in 2022, Caltrans approved the use of PLC based on your research at Oregon State University, which is actually very exciting. Could you please share a little bit about that work and what helped with the approval of low carbon cement by Caltrans?
Jason Weiss:
So while I think the Caltrans study was incredibly important, it is really just one brick in the wall of moving forward with PLC. I mean, to put this into context, the directions of this were set in place almost 20 years earlier. It began with groups at ASTM and AASHTO trying to harmonize specifications. And then there was a lot of work that was done over the course of that 20 years with groups like Thomas Matschie and his group looking at different phases, literature reviews that we did with PCA to help inform ASTM studies on limestone fineness, some of the work that Doug Hooton and Mike Thomas did on sulfate. A number of industry trials with folks like Tim Cost and Brooke Smarts, as well as an inordinate amount of technical sessions that we’ve had over the years.
I’m sure there’s a lot of folks that we’re missing in this sort of quick literature review, but all this happens… I’m saying all this to really say it takes engagement of a lot of stakeholders. We need to have a lot of different people at the table. We need to bring these ideas together. I think a few of the things that were really important there, we embraced different computational tools, and I think people saw that that was a huge ability for us to look at more than just a few mixtures. We had different groups answering questions and bringing that information together, and it really took a focused and coordinated effort over those 20 years to pull that off.
Aali Alizadeh:
That’s really exciting and actually to see that transition from research to get to where an organization such as Caltrans can approve and use the new materials or low carbon materials. That’s really exciting. Thanks for sharing that, Jason.
Let’s go to Heather. IMI is one of the largest concrete producers. How do you identify new technologies for possible application in the industry? There are so many, I think technologies that are coming to your, I think office, I know there’ll be a lot of [inaudible 00:08:17]. But what is the criteria that you have in selecting new low carbon materials or technologies, and do you have examples that you can share with our audience today?
Heather Brown:
Certainly. So I think having been an academic researcher, I had a bit of an advantage coming into industry because I understood where research really begins and what agencies are those that we should be tracking. So just like Jason mentioned, AASHTO and ASTM, I follow Federal Highways, Department of Energy, NIST, the National Science Foundation. These are all agencies that are trying to be on the cutting edge and empowering faculty and industry to look at those low carbon technologies. That body of work trickles down to research universities, ultimately making its way into scholarly journals, maybe even demonstration projects. So IMI really looks to stay engaged at levels like ACI. So there’s people giving presentations that really just emerging products. And if we’re not there at the table looking at what that availability might be, we’re missing out on a real opportunity.
Then my role really is to take that scholarly work and turn it into what I lovingly call low tech research. Low tech research is so critical to our industry. It’s really the handoff from research-based work to industry-driven practical application. So a very short-term, low tech experiment that is then kind co-sponsored by an industry outlet. Some low carbon software company, maybe a low carbon material company, working together to just really understand, is this going to work, in my case ready-mix concrete?
So a great recent example is recycled glass. That’s an emerging material that I’ve been looking at for a decade, and it’s got a large body of scholarly work, but it really is market specific. So you might have a preponderance of glass. Nashville for example, has a preponderance of glass, it’s a high consumption glass market, but nobody’s processing it for the use in ready-mixed concrete. But now we have an ASTM supporting that material, so we can put it into a concrete specification legitimately, but we don’t have a market really to support the availability of a recycled glass. So it’s a work in progress, but as IMI looks at it, we want to use it as an SEM and we know it does not have detrimental impact on strength and set and workability, but we can’t get enough of it to really house at our facilities because we’re going to run through that material at a really high volume. So while the work is there, there’s still this handoff and this availability that we really have to pay attention to.
Aali Alizadeh:
Thanks for sharing that, and a very interesting example, and love the low tech research and the notion that you had a, maybe later we can touch base on that with Jason is, most funding agencies are funding exciting and buzzwords and all of that from topics and projects. So it would be interesting to pick your brains on how low tech research can be funded later.
Perfect, so let’s go to Donn. You are promoting the use of innovating low carbon solutions that NRMCA and NRMCA is advocating for that continuously for concrete producers in the US. Can you please share some examples of bringing research outcomes in this field to the concrete industry?
Donn Thompson:
Our organization has supported research into sustainable applications for ready-mixed concrete for many years. We have a subsidiary foundation, the Concrete Advancement Foundation, that continues to support research on a variety of projects.
Some examples, sustainability plant guidelines to support the sustainable concrete plant certification program that our organization supports, which is really kind of a roadmap, a how-to guide for our ready-mixed producers to improve the sustainability of their production facilities, their operations. There’s research promoting the use of higher volumes of fly ash. That was a study that was done by NRMCA’s own laboratory to look for ways to reduce the amount of Portland cement and thereby improve the embodied carbon footprint of the mixes that could be available. Research looking into optimizing the feasibility of using crushed recycled concrete. So we already know that there’s a lot of concrete that at the end of its useful life, it gets ground up and ready for reuse. And optimizing the ability to take a lot of that material and make use of it as aggregate for new concrete, it’s just a great way of promoting the circular economy, so to speak.
And then probably most importantly is the industry support of the MIT Concrete Sustainability Hub. There’s been important work coming out of the Hub now for I guess better than 10 years, and I find it interesting that there was some mention of, how do you take research and make it more practical and accessible to the industry? And I think that was one of the challenges with the work at MIT, because they’re operating on such a high theoretical level and helping them to understand what the industry needs are and finding ways to bridge across the tremendous talent and capability that an organization or an institution like MIT can provide and what the practical realities of our industry are.
So for example, I’m very excited about work that’s ongoing at MIT to look at quantifying the impact of carbonation, the ability of in-place hardened concrete to absorb CO₂ from surrounding atmosphere. And in fact, they’re going to have a presentation coming up on May 11th, where the Deputy Director of the hub will be talking about a framework that they’ve established and they’ve been working on more accurately quantifying what the true impact is because the ability of concrete to absorb CO₂ is going to impact the footprint, the quantifying of the footprint of concrete in green building rating systems.
Aali Alizadeh:
So we’ll go to Brandon as the next panelist on this topic. With your “true zero cement product,” what has been the feedback from customers on the application of this material in the field? I know you’re trying to push this product to the market and I’m sure potential customers have a lot of questions. Do they see any obstacles in using Sublime product in the field?
Brandon Williams:
Yeah, so first let me explain what we mean by true zero. It’s sort of a tagline that we’ve used to describe our technology. So our technology is able to avoid the carbon emissions associated with the calcination process of cement, through using a electrolytic process that can take advantage of clean energy. And then we’re also able to avoid the emissions associated with that limestone calcination by using an extraction process so we can extract the materials needed to make our ASTM C-1157 performance-based cement. So that’s what we mean by true zero. But beyond that, yes, there’s skepticism for our technology, but there’s a skepticism for any new technology. Cement and concrete are very regional materials, to the point that there’s no single solution for any market. You have different cement classifications for a given market.
So the key to us having success in the market is essentially having sort of a three-pronged approach, similar to what was mentioned earlier. Internally, we do as much diligence as possible, vetting our materials to ASTM standards and AASHTO standards using ACI methods. And then beyond that, we have a third party lab, our third-party labs that are CCRL certified essentially to vet our data and make sure that we’re not acting in a isolated echo chamber. And then beyond that, getting feedback from the industry professionals, finding good partners and collaborators that are doing really innovative things in a given market to learn about their business. What are their sore points? What is a way that we can sort of seed into their business frictionlessly to the point that they don’t need to create new infrastructure, or essentially have to change the sequencing of their finish and placement crews? Because we would do a huge disservice for the industry if they had to change the way that they do things to use our technology.
So I think basically that the skepticism is important because we want all of our structures to last beyond their design life, but realistically, we have to be really two ears in one mouth with our approach and work in lockstep with the industry, essentially to vet our technology. So I guess the skepticism’s there, but having innovative partners that have done this for nearly 50 to 100 years plus, as far as experience across their business, and informing our technology is the key.
Aali Alizadeh:
Going to Lisa with tons of experience in the chemical [inaudible 00:19:14] industry. You have a lot of experience in bringing new technologies to the market. I know you have the deep innovation lab and research group and working on new technologies continuously. Where do you think low carbon technologies in particular and materials from that perspective fit from adoption and implementation perspectives, when you look at the industry?
Lisa Barnard:
Sure, there’s been a lot of great feedback from others on this topic, and I think I’ve got a little bit maybe of a low tech answer to a high tech topic. But obviously, I mean, admixtures have been around for a long time and they’ve been doing the work of kind of what we’re looking at now. Right? I mean a large part is cement reductions, cement replacement, they’ve been doing that work for quite some time. It’s just that our interest in what we were quantifying has sort of changed.
Aali Alizadeh:
So Pouria, you are working on new technologies and innovative solutions to reduce the embodied carbon in our industry. What emerging or new innovations you see are going to reshape our industry in the next few years?
Pouria Ghods:
Okay, thanks, Aali. Yeah, this is an interesting question, right? So yeah, this, I cannot answer this question from our lens. Right? So what we are doing at Giatec and also for best knowledge, right? So the way we see that, that industry may evolve over the adopting of more advanced technology. Right? So in order to bring impact, especially on the net-zero topic.
So what we see right at Giatec, so AI could be a potential technology. So to advance this industry significantly, especially if you are talking about the mix optimization or recipe of the concrete, how we can basically write those of ingredients in concrete for every job or construction project, based on the specification that we are seeing. And also, the fact that the concrete materials compared to, I don’t know, like 30, 40 years ago, it becomes more complex, where we have lots of different admixtures, new STMs, lots of new materials basically coming to this industry. And for that reason, optimization of the mix is based on the demand. Right? So different application, different use cases become more complex. And we believe that this opportunity leveraging AI to build in a way a concrete expert, especially nowadays, right?
So yeah, again, low tech, speaking of low tech. There are not too many basically people getting to this basically concrete areas, this is quite a little bit unfortunate, right? So that we are kind of having less talents coming to this industry and for that they might be opportunity. Right? So to have AI in gene, trained to the extent that can act as a concrete experts, be able to basically looking to the old recipes possible for certain application of the concrete and helping us in a real time manner, right? Even human being nowadays is really, really difficult for a human being to process lots of information in real time, whether it’s impact of the weather, traffic, delay in concrete delivery, lots of other variable that may influence the properties of the concrete. And there is I guess room for AI to fill the gap and be able to significantly impact concrete industry as a whole. And hopefully, yeah, make it much better for future generation to come.
Aali Alizadeh:
Thanks so much for sharing that perspective, Pouria. Perfect, so let’s go to the second topic for this panel discussion. Are concrete industry is responsible for 8% of global CO2 emissions? That’s massive. And I always say actually, if concrete was a country, it would’ve ranked third after US and China, in terms of annual CO₂ emissions. Think about it, that’s really huge.
With the demand for more sustainable solutions growing, I think it’s really important to look at the future and determine how we can get to the net-zero state. And a major contributor to achieving this goal is the availability of frameworks or policies and guidelines that can really accelerate the adoption of low carbon technologies in the construction industry. Let’s just start with Heather. Do you see any gap in the policies and guidelines that we have today that would cause friction in the use of low carbon technologies in our industry?
Heather Brown:
So I look forward to everybody’s responses. I’ll start with the federal Buy Clean Initiative. We’ve been hearing more about that as several states have gone to buy clean states, and I think that’s trickling into other markets on trying to head that direction.
What I’m finding though is that there’s really only limited decision-making information available to understand truly what buy clean means. And so to me, from the construction materials aspect, we’re all focused on product EPDs and right now the calculations that support a product EPD only focus on the A-1 through A-3 categories, which we know is the real material extraction, transportation, manufacturing calculations. So that’s the really intensive energy-driven kind of dark side of our industry. And I think that skewing a little bit of the true nature of what concrete, for example, can be in a cradle-to-cradle assessment.
So kind of focusing on concrete, I feel like we have been optimizing mixes. I mean, Lisa said this, we’ve been optimizing mixes 30-plus years with different chemicals, different SEMs trying to lower our dependency on straight cement as much as possible. The game has changed, the calculations are now focused on low-embodied carbon lowering CO₂, and benchmarks are starting to appear. GWP benchmarks are kilograms of CO₂ embodied in a concrete mix, and owners are looking at those numbers and they want to be better than that. They want to be better, 20% better, 50% better. I had an owner that wanted to be 70% better than the current GWP benchmark, which is very difficult to do with the current slate of materials of SEMs and chemicals that are available today. I think 1L, PLC helped move the needle a little bit, but we have a long way to go before we can be 50% better and ultimately net-zero for concrete as an example. So I think it’s going to be very difficult to improve upon this.
What I would like to see happen and where I think the gap in the policy is, is we really do need to start calculating the rest of the life cycle assessment. Concrete has always done well in life cycle assessment and we’re not quantifying that for the owners today. We have talked about concrete being a carbonation sink. So if it’s a carbonation sink, it should offset a significant amount of the actual manufacturing of concrete and cement, if we actually could quantify that for the owners. What has resulted is that wood and steel are now re-emerging as potentially low-embodied carbon materials, when if you looked at those materials over its life cycle, they would fall short I think from a total life cycle cradle-to-cradle material.
Aali Alizadeh:
Very, very interesting perspective. And actually when you look at it that way, the whole directions can change significantly if you’re not really doing that end-to-end life cycle assessment.
Donn, I would actually love to hear your perspective on this. At NRMCA, what is the approach in impacting policies, the standards and codes that are needed to promote and facilitate reviews of low-carbon construction materials? And this is something that I’m sure you have looked at and it would be great to hear your experience in that area.
Donn Thompson:
It’s really about education, from our perspective. It starts with the misconceptions that exist just when people are looking at cement versus concrete and the fact that those terms are used interchangeably and it’s the cement within the concrete that’s really the source of the bulk of the CO₂ burden that everyone is so concerned about with concrete materials.
So for example, our codes and standards team continues to advocate in favor of more robust, more resilient building codes. It really speaks to, we try and emphasize the full life cycle, kind of echoing on what Lisa was mentioning. You have a lot of competitive industries that focus only on the cradle to gate, and have done a tremendous job of really establishing the importance of the embodied carbon piece. But when you look at full life cycle, when you start considering operational impacts, and there’s lots of ways that we can demonstrate that concrete products and systems can have tremendous impact in helping to improve the energy efficiency of the buildings in which the concrete systems are used because of the inherent advantages. Thermal mass is one example, in terms of helping to reduce the mechanical loads on buildings. Looking at end-of-life phase where much of concrete is recycled.
I started to mention earlier that our laboratory at NRMCA is involved in research looking at recycled aggregates, taking end-of-life concrete and looking at the feasibility of being able to reuse more of that material so that you have a circular cradle-to-cradle approach to the use of our materials. So all of those things just help to better position our products and materials through the promotion and education that we do to just bring about more accurate assessment of the value that concrete can provide.
Aali Alizadeh:
That’s really key, as you mentioned, in bringing this to the attention of policymakers and impacting those standards and guidelines.
Brandon, have you looked at what policies or standards are required to help the market acceptance of novel cementitious systems? Sometimes if you’re looking at the latest cutting-edge advancements and technologies, policymakers and guidelines and standards might not be there. And have you reviewed what requirements are there for you to bring your low or even zero carbon material to the market?
Brandon Williams:
Well, I’m happy I’m going after Donn, because he hit a lot of good points as far as the NRMCA’s build with strength moniker. That’s been around since I’ve been in college and it’s done a lot of great work for the industry moving us past sort of prescriptive measures to more performance-based measures. Let’s do what works best to meet sort of the demand, the growing global demand, as far as sustainability.
And he’s also right about cement within concrete. So cement is about 5% of the volume in a yard of concrete and it’s about 90% of the emissions. So our technology, and I’m going to sound like a broken record in talking about the process, but we use an electrolytic process that allows us to extract a decarbonized lime and a reactive silicate to then be blended to make a performance-based cement. And thankfully. ASTM C-1157 is available as a performance-based standard. The ASTM was very forward-thinking in 1990 to create this standard to allow cement manufacturers to be innovative. And then beyond that, ACI and the International Building Code also have ASTM C-1157 as a performance-based measure for performance-based cements to come into the market.
So I would say the P-to-P or a prescriptive to performance is very important, because it allows builders to continue doing what they do best. So yes, performance-based measures all the way. We understand standards are important, just to make sure that all materials operate on a level playing field but I guess allowing builders to do what they do best is probably the best way, so.
Aali Alizadeh:
Awesome. Lisa, welcome back. I think it’s difficult virtually even to come back to the stage as you’ve put in the chat, there was a power outage, so happy to have you back.
Lisa Barnard:
Literally, yeah.
Aali Alizadeh:
On this second topic, Lisa, among your customers, there are always early doctors who would use any new technology, like they don’t care about guidelines or policy or standards. But the market majority always needs some assurance from standard organizations and building codes. And how do you think relevant organizations and authorities can help here, when it comes to low-carbon technologies?
Lisa Barnard:
Yeah, I mean, obviously in the concrete industry, the ACI is high up there, in terms of organizations that we follow, that we listened to, and we’re looking for leadership. And they recently unveiled the ACI code 323-24, low-carbon concrete, they did it at COP-28. That may be one of the first code on low-carbon concrete and I think that’s a fundamental stepping stone towards helping the industry work towards lowering its environmental footprint. I think that document should, it was rapidly developed last year and I think it’s going to be published in 2024.
I mean, I’ll jump on the NRMCA. It’s an industry association, but they’ve done a fantastic job of taking the leadership position for the ready-mixed industry in jumping on board early and developing industry-wide EPPAs and giving us the industry a place to work from, and now developing and I think Brandon Ray is going to present the concrete carbon calculator in another session. I think that’s a great step towards… One of my other comments is when I got kicked off was going to be about establishing carbon budgets on projects versus GWP limits, right? Because I think even that tends to be prescriptive when we’re putting GWP limits on certain mix designs. So this tool really allows folks to start working in this area of carbon budgets. So I think that’s an important stepping stone to start figuring out how do we, as Brandon and others have said, allow the ready-mixed producer to do what they do best? And that is promoting more performance based specifications over prescriptive and allowing the ready-mixed producer to optimize based on local knowledge.
And I think just continuing to do what these organizations do well, right? Upholding safety, reliability, consistency of concrete, but allowing for the flexibility and more rapid adoption of new technologies and materials is key.
Aali Alizadeh:
Thank you, Lisa, for sharing that. Pouria, what is your experience in working with policymakers when it comes to recommending or putting guidelines around new low carbon technologies?
Pouria Ghods:
Yeah, from my view, honestly, we can do much better, right? In the standard committees, building code organizations such as AASHTO, ASTM, ACR, to move faster. As others mentioned [inaudible 00:37:22], so having a prescriptive specification, right? So yeah, various specific mixed design in lots of market. So with the minimum cementitious material or minimum cement or even exposure classes or maximum STM limits, these are the things I would say most likely yeah, these are more kind of hindering our progress toward the net-zero. And I believe it should move faster with the trend that we see in this industry, especially in concrete industry. We’ve been in lots of pressure because of the climate change, yeah, carbon emission. Right? So to basically reduce the carbon footprint of this industry in this relatively short period of time, knowing that the adoption of any technology in this industry, it takes 15 years, 20 years. Right? So time is against us.
And I think in my personal opinion, which I have a little bit a strong opinion on this area, we can do much better and we should move faster as a member of a standard committee, to really be able to enable other technology to get into the market. Another example, so it’s more on the design side, the specification. 28 days is strengths of concrete, right? It is very normal, but I believe if we allow engineers, architecture to design to work more 56 day strengths, that by itself significantly reduce by 35%, we have some data actually our system, big amount of data supporting that. That that change by itself significantly, basically helping the industry to reduce their carbon footprint.
Aali Alizadeh:
Very interesting, thanks for sharing that. I actually see a comment from Dough Houghton, Professor Doc Houghton, that ASTM C-1157 allows for innovation in cement, but its specifiers, you don’t have trust. And Jason, you have tons of experience working with the standard organizations, DOTs, ACI, etc, in developing standards and guidelines. And it’s one thing for those standards to be in place, but another thing for building codes to adopt it and the specifiers to trust and use them. In your opinion, what do these organizations need to do to support the adoption of new low carbon technologies or even adoption of the standards that are existing?
Jason Weiss:
Thank you. I think one of the big things is we really have to take it, a German expression here is sitzfleisch, right? And it means that it’s time in the seat. It’s really understanding that in order to accomplish big things, we have to work at it and we have to stay at it. We have to work through these obstacles, and this is really becoming a big challenge when we’re in a digital world and things are changing daily. We need to understand that there is a path to go from basic research to applied research to trials, and then to go to full-scale implementation. And many times things are being lost in these gaps where people are trying to start at other places than the beginning.
Some of the steps to move things into practice are critical, but not super exciting. I’ll mention that many of our sponsoring agencies are saying, “Here’s a nine month, we want to see it implemented in nine month.” And that just doesn’t really work that way. We need to be funding the types of research that look at a product that’s going to be there to last for a century.
We need to make sure that we also, especially as it comes to test methods, get things written down on paper, get them in front of people and have people start commenting on those so we can move it forward. I mean, I look at something that’s near and dear to Giatec’s heart, the resistivity test, and this started in the ’80s with the work of McCarter and Mason and Baudouin, but it was a little Mr. Wizard-ish. It had to move into a standard and then into the DOTs and then become harmonized. And it’s taken only 40 years to get that into existence, but we need to accelerate this and we need to move this faster.
I think we also need to be open to new things like computational models. We’re moving into wide new materials that we don’t have 80 years of experience with. These models allow us to time travel to be able to predict what’s going to happen in 40, 60, 80 years. They allow us to learn about the what ifs, they allow us to refine the tests and to quantify variation.
And finally, what we really need in industry to move these things forward and in the DOTs and the agencies is a champion. I don’t know if we need Carrie Underwood and Ludacris to come and sing the champion song to everybody to make sure they understand this, but every project I’ve ever been on that has been a successful implementation, has had a champion who’s been there to make sure that they’re checking on things, they’re documenting things, they’re really helping to move the research into practice from the agency side.
Aali Alizadeh:
Thanks, but I don’t like Carrie Underwood becoming champion though. That’s a good, good, good point. Thanks for sharing that perspective, Jason.
So let’s go to the third topic, and it’s one thing to develop a new technology in the lab. As researchers, we come up with ideas every day, and sometimes these ideas evolve to become actually a research project that results in a good outcome or a successful outcome. But it’s another thing to bring that successful outcome from the lab to the market at a scalable level. You bring a technology or product or solution to the market, you face many new challenges that were not really addressed at the smallest scale. So this is sort of a scaling challenge. This transition can be very challenging from technical and economical perspectives.
So let’s discuss if our panelists have faced these challenges, and what approaches have they taken to address them? Donn, as the Head of Innovation at NRMCA, I’m sure you are regularly reviewing novel low carbon technologies. What are the technical and economical challenges you see in bringing those lab ideas, so to speak, to the broader market application?
Donn Thompson:
I think critically, you have to recognize that you’ll have more success if the products being development or developed can be distributed through the existing market infrastructure. Otherwise, the cost of entry, the feasibility of scaling the innovative systems, it gets expensive, it gets too complicated. You have a tremendous burden of selling, let’s say ready-mixed producers on the value of a new approach. I mentioned I have quite a bit of longevity at this point in the industry and construction more than, I sense more than anything, is so much about being creatures of habits. So the struggle of bringing something that’s revolutionary or helpful, you have to make it as easy as possible.
I think about the example of Portland limestone cement, which is certainly a valuable innovation for the industry. And everything I was hearing when it was first coming to market in the United States was that it would be offered as an alternative to some of the other options that we already had in place. But it’s my understanding there was quite a bit of pushback from your typical ready-mix producer because now they’re being asked to create an additional storage silo to handle yet another product, and there was a lot of pushbacks. They either didn’t feel they had the resources, weren’t ready to take the perceived risk of trying out something that they didn’t know how well it would be accepted, or just space constraints in their facilities. And so it really came down to having to adjust how the product would be brought to market. And so now it’s seen more as the baseline product instead of an additional product. And from that perspective, I think that has sped up its acceptance in the more recent timeframe.
So overall, the key is offering products that can be handled the same within our industry, work in similar ways, but they don’t represent major disruptions, in terms of bringing them to market.
Aali Alizadeh:
Thanks and very interesting point by Donn.
Brandon, could you please share your experience in scaling the soft line cement system from a small scale experimental research to a larger scale industrial application?
Brandon Williams:
I wish I could take the credit for scaling us beyond the lab, but that would truly be a disservice to our CEO and Founder, Professor Yet-Ming Chiang and Dr. Leah Ellis, they essentially started with experiments in the lab to see if they could create a electrochemical cement. And today is actually our four-year anniversary, so we spun out of MIT and now in Somerville, Massachusetts. We have a pilot that is capable of producing about 250 tons of material a year. We’re using the materials from that pilot to validate our technology in the field. We have a lot of partners. The furthest along partnership that we have and collaborators is in the Boston market, where we work with Boston Sand and Gravel to essentially trial our technology in their lab and then scale it up to do trial batches and get feedback from concrete contractors such as, SNF Concrete, can you finish the concrete? How does it behave? Can you send it down the street at three revolutions a minute and get your transit time?
Recently, we’ve been lucky enough to get a field validation with a site provided by Turner Construction, essentially where we were able to deliver our concrete to a site, see if we could pump it and place it. So I mention all of this just to essentially showcase that you need collaboration all throughout the value chain, and that is essential to scaling. You also need to hire good people and allow those people to be able to think innovatively. So I guess you hire very good and talented people, let them be as innovative as possible, and then put them through sort of an industrial funnel to create the perfect sort of feedback loop where you’re creating innovative technologies, but you’re also getting great feedback from the industry.
So beyond that, I mean, the job isn’t done. We’re currently doing diligence on a facility in Holyoke Massachusetts, that will be producing about thousands of tons of cement, and then doing some siting for a megaton facility that will hopefully be producing millions of tons of cement in 2028. So a lot of work still to do, but I guess the key to scaling is, like I said, hiring great people and then having great partners in the industry that all throughout the value chain are helping you understand and create a frictionless product.
Aali Alizadeh:
Thanks, Brandon. Lisa, when we are looking at research, it’s almost impossible to look at the variety of material interactions and job site conditions and all the different variables that may happen when you bring a new solution to the market at the scalable level. And from your perspective, what can be done to minimize this risk when you are looking at developing a product so that when it goes to the application, it’s as smooth as possible when you are bringing it to the market?
Lisa Barnard:
Yeah, I mean, I would echo a lot of what’s been said by others, but I would say that this is a very hands-on business. Our industry is concrete, right? And we talk about customer-driven innovation and being close to our customers and partnering with our customers. And so that’s really what we’re doing. Our innovation team does a great job with this. In fact, we opened a new application lab in Chicago late in 2023, and we’re building more across North America and different regions to be closer to our customers and materials so we can test, tweak, scale much more efficiently. We utilize those labs to test local and new materials, things that keep coming up, [inaudible 00:51:14], ground glass that Heather mentioned, with our ad mixtures using mortar mixes, or as we call, mini mixes. We can do that at a small scale and be quick and not a lot of waste.
It allows us to ID and predict more successful formulations and mix designs so then we can partner with customers in the field to put those things in production scale, because we’ve got to do both. Right? But if we can go to the lab in a small scale and test things, we can get further faster and then take it out into the field. I mean, we use that process to bring our strength enhancer environments, SE to market more rapidly, to meet increasing demand for cement reduction products. And that’s really how we’re going to keep trying to drive going forward, is we have to be hands-on, but how do we be efficient about it? And we’ve started this process and having these application labs closer to our customers really makes a lot of sense, particularly with the speed at which materials and the industry is evolving to meet these low carbon challenges.
Aali Alizadeh:
And thank you Lisa, and going to Pouria, many experiences in commercializing new products. What lessons you can share with us and getting that product market fit, so to speak, right when you bring new technologies to the market?
Pouria Ghods:
Yes, yeah, we learned by doing lots of mistakes over the past 15 years. So how to bring an idea from research from the bench all the way to the application and make it really a commercial success basically.
A few things that could be helpful. So people who are looking at commercialization of any ideas, one is just breaking the basically steps into as small as possible. So for phases, phase one could be pilot, proof of concept pilot, MVP, early access customers. So what you learn that if you have more smaller steps and also to have a go, no-go kind of condition. So you have a better chance of, with the limited resources you have to advance the product concept or technology further toward the commercializations. With the understanding that at any point, so yeah, you may need to quit the project at any of those steps. That would be one thing I guess have been helpful for us.
And the other, second one, especially related to net-zero, green clean technology in this industry, especially in construction industry. Clean tech, yeah, I guess the key for adoption, knowing that this industry has been very slow adopting the technology, right? No offense, I’m coming from this industry, is more looking at the economy. So making sure that as much as possible, sometimes might not be possible, that you are not adding significant cost to the solution or adding significant cost to the project or to the materials. And if there is a way that you can make it a little bit more cost effective, any new clean tech solution, that would be another driver so that you can rely on for adoption of the technology or make it more successful when you are trying to commercialize it at the very largest scale.
Yeah, this is a kind of definition of product market fit. Yeah, there are lots of other criteria to make sure that yeah, you get the product market fit as soon as possible. But these two things I thought are related or more relevant to this conversation.
Aali Alizadeh:
Thank you for sharing that Pouria. Jason, and when we look at the market, we obviously see the successful products and the ones that made it to the market and at a scalable level. But I’m sure in your research and academic experience, there are examples of exciting low carbon technologies in particular that maybe didn’t make it to the market. And I would love to hear what barriers you see as being the barriers that prevented the larger scale adoption of those two exciting projects.
Jason Weiss:
So I think when we start to look at some of these barriers, I think one of our biggest barriers as an industry is we really aren’t open to a lot of new things. I mean, a few of us, if we thought we broke our arm, would go to the doctor and say, “Instead of doing x-rays, just give me two of your best leeches.” But we do this every single day when we order concrete. People go in and order a seven bag mix or do things like that. We have a lot of technologies that we could be using more of today that are off-elf, whether it’s SCMs, and even what people are calling new SCMs, like natural pozzolans. Natural pozzolans were used 100 years ago and we have a history of these working really well, but we’re restarting the whole thing. We’ve had several technologies that have been really slow to adopt. We’ve done a lot of work over the last 30 years on ways to make our concretes more durable or to model that, and we haven’t really been using that.
As far as some of the innovative new technologies. The ability to carbonate solids instead of hydrate and react them with water is very, very exciting, and there’s several companies in that space. Alternative binders like the one Brandon’s talking about are really exciting and have the opportunity to be a direct substitution in the market. We’re seeing lots of new binders with calcine clays, high-aluminous slags and limestone, as well as innovative SCMs. I think the biggest challenges though that we see are one, the volumes. Many times people don’t understand the volume of material that it takes to keep plants running and keep making sure that people have enough to do the project.
And to follow on Doug’s comments. Many times we either don’t have the right specification or we don’t trust the specification, and it’s a little bit surprising because it’s like going to a five-star restaurant and not trusting the chef to make the concrete. We want that five-star chef to do it, but then we’re going to ask Emeril about, what was his exact recipe? How long did he cook things? Did he do it this way? Did he do it that way? And I think we need to either decide if we’re going to move into performance, step out of watching the recipe, and allow the people who are experts to really do it.
Aali Alizadeh:
And Heather, you have probably tried many novel solutions in the ready-mix industry. What do you think innovators need to do to make the low carbon technologies a fit at a scale before they bring them and pitch them to you?
Heather Brown:
So Donn and Jason definitely touched on this, but I do feel like the low carbon companies need to have a good understanding of batching and production and the equipment needed. There are limitations in our capacity to put a product, let’s say in a silo or a bin or even a tank. And so when products come to us in buckets and bags, it can be cumbersome. It’s not undoable, but it is a cumbersome process, it slows everything down, it’s a safety hazard. And so if companies could engineer a conveyance system that is ideal for their product, maybe even offer up a portable pig or some sort of conveyor belt, that would help increase the rate of adoption.
I’ll give you a good example and a bad example. A good example is companies have come to us with fiber dispensing equipment, which has been revolutionary. We’ve been using fiber for decades, but now we don’t have to throw bags, we don’t have to put guys on top of trucks. We don’t have the type of inventory necessity. We can put a super sack right on the fiber dispensing equipment and run through fiber very quickly. It’s less mistakes, we could deliver concrete faster. Our yards per goes up, it’s less manpower, and we’re still lowering the embodied footprint because we’re using less labor in the field to put down light gauge steel. We’re using less steel in general, and that proves to be really valuable.
A bad example, or an example that’s not quite made it to that production level is graphene. Graphene is a great product that is proving itself in the lab. There’s a lot of researchers looking at graphene as a flexural enhancement to concrete. But I’ve managed graphene in the lab and in the plant, and it is a monster to work with. It’s very sticky, it goes airborne immediately. So there’s some engineering that needs to be done, some conveyance that needs to be done to get graphene into a form that we can use at the plants. But a great product, would love to see it go to market and scale up, but we’ve just got right now some managing issues with that product.
Aali Alizadeh:
Interesting. Yeah, sometimes that sort of yield and getting that product to market can prove really challenging at a scale.
Okay, I think unfortunately we’re running a bit over time. I would’ve loved to go through the next topic on the EPDs, but unfortunately we don’t have time as our next speaker and the keynote speaker is here.
I really would love to thank everyone who joined this panel discussion. And as we are concluding the topics we had for today’s panel discussion, I’m sure the audience have some questions. You can put them in the chat and the panelists can stick around and answer those questions if they’re in the chat. And again, thank you so much to our panelists for sharing their insights on this topic. I hope the audience enjoyed the discussions, so please stick around for the keynote that’s going to happen in this room. And I hope you’ll also enjoy the rest of the talks throughout the day at the Net-Zero Construction Conference. Thank you again, and have an awesome day.
Other Related Episodes
Episode 55 |
February 27, 2025
Optimizing Concrete from Fleet to Finish
In this latest episode, host Sarah McGuire speaks with Chris Wurtz, Division President at Digital Fleet, about the impact of data-driven decision-making in the ready-mix concrete industry. With expertise in fleet tracking technology, Chris sheds light on the challenges and opportunities of controlling what he calls a “factory on wheels”—the mixer truck. He explores the biggest obstacles facing producers today, from data limitations to inefficiencies in delivery, and highlights untapped opportunities to improve performance. Chris also discusses the vision behind Digital Fleet’s partnership with Giatec on MixPilot and how this integration is helping producers gain better control over their operations. Tune in for an insightful conversation on the future of ready-mix operations and how collaboration between technology providers is driving industry-wide transformation. Don’t miss this engaging discussion!
PLAY
Episode 54 |
February 6, 2025
Smarter Water Management for Safer and Greener Construction
In this episode of The Construction Revolution Podcast, Steven Rossi sits down with Yaron Dycian, Chief Product and Strategy Officer of WINT Water Intelligence. With over 25 years of experience driving strategy and innovation at leading companies like IBM and RSA, Yaron is leading the charge in AI-powered water management solutions. Tune in as Yaron shares the story of WINT, explores the rising challenges of water damage claims, and discusses how advanced monitoring and leak mitigation technologies are shaping the future of construction. From preventing costly damages to meeting sustainability standards and lowering carbon footprints, this episode offers valuable insights into how construction companies can stay ahead in a rapidly evolving industry.
PLAY
Episode 53 |
December 12, 2024
Unlocking AI’s Potential in Construction
In this latest episode, host Sarah McGuire sits down with Sean Devine, Founder and CEO, XBE, to explore the transformative role of AI in the construction industry. With a background in logistics and technology, Sean brings unique insights into the challenges and opportunities surrounding AI adoption in construction. Sean highlights untapped opportunities and discusses how XBE is leading the charge with innovative solutions, including AskConcrete— a groundbreaking answer engine powered by decades of NRMCA data, designed to tackle complex questions about ready-mixed concrete. From identifying industry limitations to exploring what companies need to do to embrace AI effectively, Sean offers a compelling roadmap for innovation. He also shares his journey in founding XBE and his mission to optimize heavy construction operations with cutting-edge technology. Tune in to gain valuable insights into how AI is shaping the future of construction. Don’t miss this enlightening discussion!
PLAY
Want to Be a Guest Speaker, Sponsor, or Just Have a Question for Us? Fill In the Form!