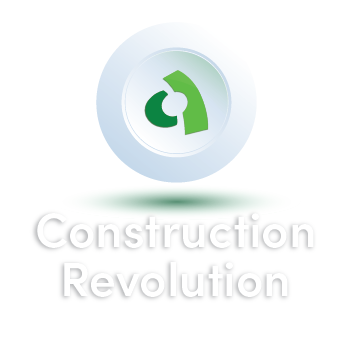
Episode 54 |
February 6, 2025
Smarter Water Management for Safer and Greener Construction
In This Episode
In this episode of The Construction Revolution Podcast, Steven Rossi sits down with Yaron Dycian, Chief Product and Strategy Officer of WINT Water Intelligence. With over 25 years of experience driving strategy and innovation at leading companies like IBM and RSA, Yaron is leading the charge in AI-powered water management solutions. Tune in as Yaron shares the story of WINT, explores the rising challenges of water damage claims, and discusses how advanced monitoring and leak mitigation technologies are shaping the future of construction. From preventing costly damages to meeting sustainability standards and lowering carbon footprints, this episode offers valuable insights into how construction companies can stay ahead in a rapidly evolving industry.
Host
Steven Rossi
Marketing & Events Lead, Giatec Scientific Inc.
Guest
Yaron Dycian
Chief Product and Strategy Officer, WINT Water Intelligence
Podcast Transcript:
Steven:
Hello there and welcome to the Construction Revolution podcast. My name is Steven Rossi, and here on the show we explore the latest trends, technologies, people, and organizations that are revolutionizing or disrupting the construction industry and are changing what the industry will look like tomorrow. Today we welcome Yaron Dycian, the Chief Product and Strategy officer of WINT water Intelligence. Yaron brings over 25 years of experience in driving strategy, building disruptive products, and leading market execution at both innovative startups and Fortune 500 companies. He has held leadership roles at companies such as IBM, RSA, and Consumer Physics. Join us as we explore how WINT is leveraging AI and advanced technology to revolutionize water management in construction, helping to mitigate damage, reduce costs, and support sustainable initiatives.
Hi Yaron, welcome to the Construction Revolution podcast. How are you doing today?
Yaron:
Good, good. Hi, Steven. Thanks for having me. I’m doing great.
Steven:
That’s great. We’re excited to learn more about you and WINT, and I’m personally excited to learn a lot more about water management, and especially in construction. It’s not something we’ve covered here yet, so I’m excited to learn a lot more about the topic. So why don’t we start off and can you tell me about WINT and their solutions for the construction industry?
Yaron:
Yeah, absolutely. So we provide solutions that are designed to mitigate water leaks and damage, and at the same time improve the facility or the construction projects, water sustainability, and sustainability in general. The solutions, technically … They seem quite simple. It’s a valve in a meter connected to a controller, the controller reads the water flow data in real time on a continuous basis, it uses various algorithms, AI machine learning, and similar technologies to understand what’s normal at the location, and when it identifies an anomaly, it creates an alert. It alerts the site team and it can shut water off automatically, and that is essentially the solution.
Steven:
Nice. Can you tell me about the typical sources of water waste and water leaks and damage that you’ve seen on a construction site that you aim to mitigate?
Yaron:
Yeah, so let’s start with damage. Damage is the big thing that really concerns anybody involved in construction, whether it’s the GC, the developer, the MEP team, or the insurer. They’re all worried about this and the water leaks, the damage comes from multiple sources. I’d say typical bad fittings. A mid-sized building will have thousands of fittings. All we need is one to go wrong and it’ll leak away unseen if it happens during late hours or during the weekend. So that’s one source.
Another source is just a tap left open. Oftentimes we’ll see in a construction project that the water discharge location, the hole in the bathtub or the sink or whatever, they will be clogged for some reason, happens on construction sites, and then just a tap running will cause massive damage. In fact, I’ve seen tens of millions of dollars of damage from such a specific incident. So these are two typical ones.
I’ve seen intentional damage, disgruntled employees and such. That does seem to be a problem. Workmanship is oftentimes the cause. So you’ll see all sorts of root causes in all sorts of locations, and these are some of them. Another source of issues, as you mentioned, is water waste. Water waste on construction sites is more often than you’d think, and I’ll give you two examples. One site will often have a tank that accumulates water for use during the day. I’ve seen situations where these tanks that automatically fill up have a problem, stop fill mechanism, floater valve or whatever that is, and it’ll just let water in, let water out, and it’ll continue on and on for months and even years, as long as the project goes on. I have a customer who … And nobody sees it doesn’t show up, nobody sees the water bills. There’s just really, it’s totally invisible. I’ve seen one site where had this gone on until the end of the project, $110,000 would’ve gone down the drain. Insane.
Another source is, surprisingly enough, restrooms, a toilet. Now many times when you commission water in the building, the toilets may be stuck, and that may go on for a very long time. Amazingly enough, a stuck toilet like that can run at between 100 and 200 gallons an hour. Think of that running for three months from water commissioning until handover, until somebody actually enters that office restroom or the flat. So you’re looking at big numbers, and they accumulate to tens and … Not often, but sometimes even over $100,000 a year.
Steven:
Wow. Yeah, that’s definitely eye-opening and a lot more than I was expecting. So how does WINT’s technology and your solutions, how do you prevent those sort of things?
Yaron:
Yep. So the trick is to be able to monitor water flows at critical locations at the site. You could put one right at the entrance. If it’s a small site, that’ll do. But usually if you have a bigger site, it becomes a little inconvenient and inaccurate to identify the issue just at the entrance. So we distribute and install meters, valves, and controllers at multiple locations. We have MEP engineers who are experts at what we do, and they will be able to consult the customer and say, “These are the locations where you should install these systems.”
Systems get installed, and then by monitoring water flow in real time, you can actually identify that something is abnormal. And that anomaly … Essentially when we say … AI is a big word, it means many things to many people, and the most impressive form of AI is the large language models that we’re all now experiencing storm the world. We’re a different variant of AI. Not as spectacular from a visibility point of view, but AI really helps us identify anomalies in a very effective way. And so we identify these anomalies, or the AI does that for us, and once the anomaly has been identified, you can now take action alerts, stop valves and so on.
Steven:
Nice. Okay. And then you mentioned there’s obviously various people who’d be interested in having this and get value out of preventing waste to cost like this. So I’m wondering who is typically your customer in the construction situation? Is it the developer or the owner? Is it the GC? You had mentioned insurance companies who will have an interest in making sure there’s no damage. So yeah, who is the one that typically buys it, and then also who are the ones that they are using it every day?
Yaron:
Okay. Yeah, as I think you mentioned, this is really an ecosystem. The most worried are the insurers, because they have to pay up if something happens. And so at various levels and various forms of requiring these types of solutions, insurers will do that. I can tell you, in the UK where the problem has really mushroomed to untenable levels … I know of insurers in the UK who actually stepped out of the builders risk market because they couldn’t take the water damage anymore. So it became so big that in the UK, insurers grouped together, they let a group of expert engineers come up with regulation that they will now require across their construction portfolio.
In the US it’s not that advanced, but still, many insurers are now requiring it for projects over a certain size, for customers of a certain level of risk. Wood frame is even a bigger risk because water flowing into a wood frame building could really cause massive damage. It damages the foundations of the building. It’s not just the internals or the finishings.
So insurers are one. The GC, naturally. They’re in charge of the project, they’re in charge of construction. And oftentimes the MEP team will be requested to actually use it, because this is really their expertise. So the GC will say, “Look, Mr. MEP, you need to take this and use it. We bought this for you, or you buy it for us,” or whatever. But the MEP team will oftentimes be the ones actually using the product on the ground.
Steven:
Nice. Okay. That makes sense.
So when we were looking into WINT and to some of the previous podcasts you’ve been on, we saw that you previously stated that particularly with regard to safety, water is the new fire in the construction sectors particularly. So can you explain that and what makes preventing water damage as important as fire safety?
Yaron:
Yeah, absolutely. So the source of this is insurance companies. And when they say … This is not my or WINT’s statement, this is a quote from insurers. And the reason they’re saying this is that many tens of years ago, fire, from an insurer point of view, was the biggest source of losses. It was common in construction sites. It was very damaging and it was extremely costly for them. Fast forward that many tens of years and they pretty much managed to solve that problem. Not 100%, there’s never 100%, but it is no longer their number one source of issues. And the number one issue has become water, with massive damages, impact on profitability of the insurance company. And so from that point of view, the losses incurred by insurers, it is the new fire.
Steven:
Right, okay. Makes sense. So as we’re into winter months, especially here in North America and Canada, here where we are it’s obviously very cold, and I’m sure that leads to increased risk for water damage, especially on construction sites where things are exposed and stuff. Can you tell me about what are some of those challenges that you see during winter/cold weather construction and how WINT’s solution helps in those cases as well?
Yaron:
Sure. Look, I think it’s quite obvious. The number one difference between winter and other seasons is stuff freezes. And when things freeze in pipes, when water freezes in pipes, you oftentimes will get a pipe burst, which when defrosting will result in water damage.
It’s interesting, we are in winter now, and I’m just coming off of a customer conversation. That customer, as a mitigation, is constantly running water through their pipes. Naturally, that’s what people do. That creates all sorts of issues, like now you have continuous flows. How do you know that these continuous flows are legitimate, or when do you need to stop them? If you stop them, you’ve got the mitigation gone. Instead of helping, you’re actually causing damage. So you find yourself in an interesting spot there. You came to help and you actually disrupted the operation.
So these are some of the things to keep in mind, and I think it’s a matter of experience combining technology and process. How do you deal with these situations in winter? How do you optimize your protection, whether water is running continuously or not, and how do you make sure that this does not disrupt rather than help? So that’s the kind of thing that we’re working on during the winter.
Steven:
Right. And I guess your solution, whether they choose to continuously monitor water or not, you’ll be able to detect the changes in either case. Is that right?
Yaron:
That is correct.
Steven:
So you’ve touched on the other aspect of the solution, which is sustainability, which sustainability is a huge topic in construction right now. Pretty much in everything, but definitely in construction, as we’re trying to catch up in that aspect. So how does WINT help in the sustainability efforts and help companies to meet those targets and stuff that they’re either they’re setting for themselves or governments are setting for them?
Yaron:
Yeah. So water and sustainability. So water has essentially two legs on which it stands in relationship to sustainability. The first is water is becoming a scarce issue. We all saw the disastrous fires in LA. They did not have enough water, and that’s not for no reason. That’s because water is becoming scarce. That’s because, I’m assuming, the LA area uses water from Lake Mead, which is drying up, and there’s a whole set of problems coming up from lack of water and reduction in water reservoirs.
So amazingly enough, we say that on the one hand, and on the other hand, a quarter of the water that goes into commercial buildings is just waste. It’s inefficient use, it’s a tap lift open here, a misaligned cooling tower there. A million … I call it death by a thousand cuts. There’s a million little things, none of which sounds impressive, and together they accumulate to 25% of water. That’s a lot. So we’re just depleting the already depleted reservoirs, let alone just paying for it for no good reason, and it does add up, and water prices are rising, so this is becoming more and more expensive. So that’s one side, just a pure waste of water and the impact on the environment.
The second thing is water does not arrive at our tap magically. It takes pulling it out of the ground, or the lake, or desalinating it. It takes distribution, it takes filtration and cleansing, and then it gets to you and you use it and then it goes back into a sewage treatment facility. Again, distribution. The sewage treatment facility is a big emitter of greenhouse gases on its own. Altogether. Water has a footprint. When we drink a cup of water, we emitted that much carbon or greenhouse gases into the atmosphere. And so by reducing the amount of water that we use and waste, we not only save money and help reservoirs, we also reduce the root cause of this whole global warming issue and we reduce the amount of carbon emissions that we emit.
Steven:
Right. Yeah, no, that’s a good point. You got to consider more than … It’s more than just using the water itself. It’s everything that goes into that as well.
All right. So I’m wondering, looking ahead as the product and strategy officer, if there’s any exciting things that you’re working on that you could tell me about, or how you see wind and the solutions evolving over say the next five plus years?
Yaron:
Sure. I think you’ll see us evolving in two areas, and I won’t be too detailed, but water is not just water. Water is also energy. Most of the energy used in buildings actually comes in through water, whether it’s large commercial buildings, or large multifamily buildings, will heat or cool, whichever HVAC side of things it is, it happens through water. So you can figure out energy through water, you can identify energy and efficiencies through water, and there’s a lot of other attributes related to water that you want to manage in your facility. Quality. We’ve all heard of these scary tanks where a dead mouse may be sitting or swimming, or whatever you want to call it. So water quality is an issue. There’s a lot of attributes of water that people really care about, and it’s just been a non-managed resource forever and ever. We started managing it through these two specific aspects of sustainability and damage, but there’s a lot more to water. So that’s one area you’ll see us evolving in. And the other one is other liquids. The technology that we have is applicable to a very broad set of liquids. It actually doesn’t even care what liquid it is. It knows how to look at flows and learn things about those flows through that. And so you’ll see us doing things in other flow types.
Steven:
Nice. That’s exciting. Going away from WINT specifically, I’m sure in your work, talking with customers, being on job sites, all the different things, you’ve come across a lot of other emerging technology for different aspects of construction, apart from just water management. So I’m wondering if there’s any of those that excite you that you’ve seen that are either starting being implemented or you’ve seen that aren’t even implemented yet that excites you about the future of construction?
Yaron:
Yeah. Look, I think one of the reasons construction has not been a big adopter of technology is because it’s a very complicated environment where things are quite unpredictable and it was just difficult to apply technologies to them. I think this is changing a lot through AI, because AI is very good at complicated environments, which precooked algorithms or instruction sets are not very good at. So I think we will see a lot of innovation coming through AI.
Specifically, I’ve seen interesting things in camera usage, knowing if your site is up to safety standards, knowing if your site is up to plan. I’ve seen technologies where people walk around the facility with a camera on their hat and it knows if somebody made a mistake in construction relative to the plans. Now if you think about it, that is a hellishly difficult task. Here’s the guy walking around a non-finished construction project, and I need to look at the plans and identify that there’s a mistake. A person could do it if you were a real expert and with a lot of work, and I’m seeing that happen. So these are game changers.
The savings from prevention of mistakes, or early catching of these mistakes is a game changer. I’ve started to see robotics technologies, I think it’ll take more time, but I’ve seen things … Maybe actually it’s more of an operational building thing, but high-rise, window cleaning. Mundane as it is, it’s an expensive task. It’s difficult. There’s crazy return on investment by using robots that do this, and I’ve seen a few really exciting things that do it well. It’s actually a very difficult technological challenge. But when done well, it’s surprising how much money it can save and how much better it can make the building. So these are just two that come to mind off the top of my head.
Steven:
Yeah, absolutely. Yeah, that’s great. It’s interesting. I like asking that question, sort of seeing what different people think. Yeah, we’ve had a few companies in terms of camera and stuff that we’ve talked about. Yeah, it’s definitely … I think to your point, same thing with what you’re doing, like preventing issues, flagging those before buildings get finished or anything. So we’re preventing those longer term issues, making everything last longer, which helps longer term in all different aspects as well.
All right. So to wrap us up here, if someone wants to get started with WINT, where should they go and what does that initial process look like?
Yaron:
It’s as simple as getting to our website. There’s a contact us form. Contact us. We’ll get back to you. The process will include understanding your needs. Initially at a high level, then at granular plans level. We will propose … We will discuss the merits of the different types of deployment that can be done. Because this is an engineered solution. It’s not like there’s one solution fits all. You could always go to the very basic, here’s one of the mains and maybe one on the temporary line and one on fire. That’s fine. It’s main line … Main temp fire is okay, but we will discuss all the options, where to install, what that gives you. And at that point, customers choose what they want for their site, whether they want to use it only for construction, whether they want to consider use for operational stages. So basically we’re seeing quite a trend these days of adding water management solutions to building plans and embedding those in the fabric of the building. So you have a waterproof, watertight, and water sustainable building for generations.
Steven:
Great. Yeah, makes sense. So I guess just to follow up question to that. In those situations where obviously there’s value for this technology more than just for construction, as you mentioned, are you just installing this at the beginning during construction, and then the GC uses it and then it gets transferred over to the facilities management? Or are you installing a different set of systems for each use case?
Yaron:
Yes. So the deployment will be slightly different for the same facility, whether it’s construction or operational. Locations, density of systems and so on will not be identical. We can install either during construction, plan it pre-construction and install during construction, or we do retrofits. We definitely have retrofit customers. Empire State Building is a customer, for example, and I can guarantee we were not there when they built the place. So it’s an example. We do both.
Steven:
Okay. Yeah, makes sense. Awesome.
All right. Well it was really nice talking to you, Yaron, and to learn more about water management and about WINT. Thanks for taking the time with us today.
Yaron:
Thanks a lot. Thanks for having me on your podcast. Appreciate it, and it’s been fun. Thank you.
Other Related Episodes
Episode 55 |
February 27, 2025
Optimizing Concrete from Fleet to Finish
In this latest episode, host Sarah McGuire speaks with Chris Wurtz, Division President at Digital Fleet, about the impact of data-driven decision-making in the ready-mix concrete industry. With expertise in fleet tracking technology, Chris sheds light on the challenges and opportunities of controlling what he calls a “factory on wheels”—the mixer truck. He explores the biggest obstacles facing producers today, from data limitations to inefficiencies in delivery, and highlights untapped opportunities to improve performance. Chris also discusses the vision behind Digital Fleet’s partnership with Giatec on MixPilot and how this integration is helping producers gain better control over their operations. Tune in for an insightful conversation on the future of ready-mix operations and how collaboration between technology providers is driving industry-wide transformation. Don’t miss this engaging discussion!
PLAY
Episode 53 |
December 12, 2024
Unlocking AI’s Potential in Construction
In this latest episode, host Sarah McGuire sits down with Sean Devine, Founder and CEO, XBE, to explore the transformative role of AI in the construction industry. With a background in logistics and technology, Sean brings unique insights into the challenges and opportunities surrounding AI adoption in construction. Sean highlights untapped opportunities and discusses how XBE is leading the charge with innovative solutions, including AskConcrete— a groundbreaking answer engine powered by decades of NRMCA data, designed to tackle complex questions about ready-mixed concrete. From identifying industry limitations to exploring what companies need to do to embrace AI effectively, Sean offers a compelling roadmap for innovation. He also shares his journey in founding XBE and his mission to optimize heavy construction operations with cutting-edge technology. Tune in to gain valuable insights into how AI is shaping the future of construction. Don’t miss this enlightening discussion!
PLAY
Episode 52 |
November 14, 2024
Advancements in Low-Carbon Construction Technologies
Join us for an engaging and insightful panel discussion from 2024 Net Zero Construction Conference, hosted by Aali Alizadeh, Ph.D., Co-Founder and CTO of Giatec and Technology Chair of The Net Zero Construction Conference. This episode dives into groundbreaking advancements in low-carbon construction technologies, highlighting both the promising opportunities and the significant challenges involved in their industry adoption.
Our distinguished panel of experts features: Professor Jason Weiss from Oregon State University, Heather Brown, Ph.D., Vice President of Quality Control/Quality Assurance at Irving Materials Inc. (IMI), Donn Thompson, Senior Director of Building Innovations at the National Ready Mixed Concrete Association (NRMCA), Brandon Williams, Business Development Manager at Sublime Systems, Lisa Barnard, Sustainability & EPD Program Manager at Chryso Saint-Gobain, and Pouria Ghods, Ph.D., Co-Founder and CEO of Giatec. Together, they offer a wealth of knowledge on the latest advancements in sustainable construction, sharing how innovative materials and solutions are transforming the industry.
Don’t miss this opportunity to learn from industry leaders as they share actionable insights and strategies that can drive meaningful change in the construction landscape.
Want to dive deeper into conversations like the ones in this episode? Join us at the Net Zero Construction Conference 2025 on March 19-20 in the Virbela Metaverse! Experience two days of expert panels, innovative insights, and networking opportunities focused on low-carbon construction technologies. Learn more and get your tickets on the N0CC website!
PLAY
Want to Be a Guest Speaker, Sponsor, or Just Have a Question for Us? Fill In the Form!