PROBLEM
When beginning the construction of a large wharf in Nova Scotia, Dexter Construction—the largest civil contractor in Atlantic Canada—was looking for a product that would help them avoid delays due to temperature fluctuations, especially during winter. Delays not only cost valuable production time in their schedules, but also affect the quality of the concrete structure.
With a reputation for high-quality, world-class service spanning 40 years and a corporate-wide commitment to safety and efficiency, they needed a reliable, efficient solution for their cold weather concreting needs.
That’s when a simple Google search yielded Giatec’s SmartRock—a completely wireless concrete sensor that is fully embedded in the concrete (on the rebar) and relays real-time temperature and strength data instantly to the crew’s phones every 15 minutes.
SOLUTION
Giatec’s proactive approach, coupled with its unique wireless maturity monitoring technology, proved to be just what Dexter’s Quality Control General Manager, Sheldon Roach, was looking for. He decided to test out SmartRock for several reasons:
- The simple installation process
- The appeal of fewer cylinder break tests
- The ability to take temperature and strength readings and view results even when a QC Manager was on vacation
- The ability to share data with project owners, investors, and consultants
- The thorough training and responsive customer support offered by Giatec
While the construction of the large wharf was a government project that cannot be detailed in this case study, Dexter confirmed that they used 80 sensors in total for the project, installing 3 sensors per 10-foot wall, in order to accurately track concrete curing.
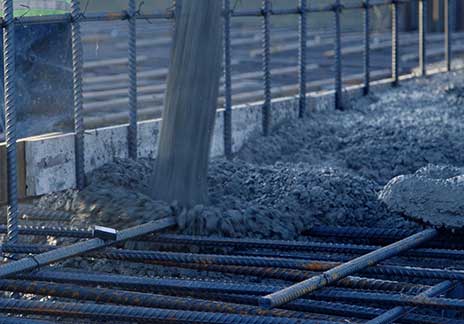
RESULTS
65% Fewer Break Tests
According to Roach’s tests, data from the SmartRock sensors was consistent with the data from the broken cylinders. All sensors were within 1 MPa (145 psi) of one another and matched the results of the field-cured cylinders, proving the accuracy and reliability of the wireless temperature and maturity sensors.
“Typically, we have three field-cured cylinders, and now, we only have one—every second or third pour,” stated Roach. This also eliminated extra costs of having a third-party consultant visit the jobsite. ”We did not need to have a consultant come get the cylinders, transport, test them, and so on,” he continued.
2 Days Saved per Pour
By cutting down to only one cylinder instead of three—in addition to having access to real-time data—the Dexter team was effectively able to save two days per pour and strip forms ahead of schedule.
Reduced Risk of Thermal Cracking
With accurate temperature data at their fingertips, Roach and his team were able to monitor temperature differentials in real time and determine when to add and/or remove heat from the concrete in order to prevent thermal cracking and ensure quality.
Easy and Faster Data Sharing
Using SmartRock, the Dexter team was not limited to one person or device to access sensor data. Rather, they were able to collect this information when they were on site and were able to share progress with the project owners and consultants instantly. This saved them time and provided a level of comfort to all parties involved.
“We weren’t limited to a piece of equipment to access the data.”
Sheldon Roach, Quality Control General Manager, Dexter Construction
Preserving High-Quality Structures While Saving Time and Resources
For QC General Manager Roach, quality is always the priority, especially during the unpredictable winter months, which is why going forward, he hopes to use SmartRock maturity meters on all of his projects