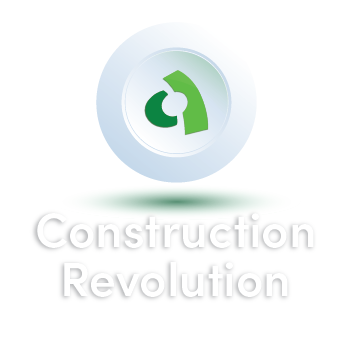
Episode 36 |
January 11, 2024
Lessons in Construction Safety
In This Episode
In this episode of The Construction Revolution Podcast, we sit down with Terry Dussault, Founder of Yellowknife Consulting Services. With over 25 years as a corporate environmental health and safety professional, Terry has become Southern California's foremost safety expert.
We will focus on the importance of safety and compliance on jobsites. Tune in to learn about the best practices that you and your team can implement to make your jobsites safer for everyone. Discover how Terry's expertise in various safety regulations has shaped his career and influenced the construction landscape.
Host
Steven Rossi-Zalmons
Marketing & Events Lead, Giatec Scientific Inc.
Guest
Terry Dussault
Founder, Yellowknife Consulting Services
Podcast Transcript
Steven Rossi-Zalmons:
Hello there and welcome to the Construction Revolution Podcast. My name is Steven Rossi, and here on the show we explore the latest trends, technologies, people, and organizations that are revolutionizing or disrupting the construction industry and are changing what the industry will look like tomorrow. Today on the show I’m speaking with Terry Dussault, the founder of Yellowknife Consulting Services. With over 25 years in environmental health and safety, Terry is Southern California’s top safety expert. His expertise spans numerous regulations in a variety of industries including construction, oil and gas, manufacturing, and aerospace. Join us as we explore Terry’s journey in workplace safety and to learn what you can do to help create a safer construction industry for everyone. Hi, Terry. Welcome to the show today. How are you doing?
Terry Dussault:
I’m great, Steven. Thanks for having me. I really appreciate this opportunity.
Steven Rossi-Zalmons:
Yeah, absolutely. Thanks for joining us. I’m excited to learn more about you and talk safety and construction today.
Terry Dussault:
Okay, excellent.
Steven Rossi-Zalmons:
So I guess we’ll dive right in. If you can tell us how you got started working in workplace safety.
Terry Dussault:
I didn’t really ever intend on being in safety. I first was introduced to it, not because I wanted this role, but I worked for a company that was founded by John Wayne. And one day I showed up at work and there was a notice that I was promoted to the safety manager. So it was a small manufacturing company. They built oil water separators for ships. I was the production manager there in the manufacturing side and that the president of the company thought it would be a good idea to drop me into the safety manager position. I’ve kind of said in the past, I didn’t pick safety. Safety picked me, and this was a reoccurring thing that kept happening at different companies that I would go to and somehow it would always end up in some a safety position. So that’s kind of how it got started.
And then back in 2000 to 2002, I was doing a lot of work for oil companies and they had a very strict safety policies and programs that you had to follow if you wanted to do work for them. And so I got nominated to go to their training school and anyway, and it evolved from there. So that’s how I got into it and I’ve learned to like it. It’s like eating your vegetables, but I’ve done a lot of field work, worked in the environmental industry and construction, and I’ve always been very mechanical. And so a lot of the safety stuff that’s been required over the years comes easy to me. So I’ve really learned to love it. I have a passion for it, and I really truly care about people and want to prevent them from getting hurt at work or prevent companies from having what I would call losses that are associated with workplace accidents.
Steven Rossi-Zalmons:
Yeah, absolutely. Yeah. No, that’s great. I mean, you’ve been doing it for a long time and as you mentioned many different industries, so I’m glad that you like it. So based on that, you touched on, you’ve worked in manufacturing, oil and gas, bit of construction. I’m wondering specifically as we’re focused on construction today, what’s been your experience on the construction side?
Terry Dussault:
Yeah, so in construction it’s been mainly underground type stuff like pipeline, and in the last few years it’s been more vertical construction, like building wastewater treatment facilities and things like that. But it’s not really the type of construction where we’re building high rises and that kind of thing. It’s more concrete excavating sites that are contaminated and building treatment systems and things like that. But the hazards are all the same regardless of what industry you’re in. But with construction I have a lot of experience around heavy equipment.
Steven Rossi-Zalmons:
Yeah, for sure that makes sense, that yeah, especially in those types of projects would have more risk than your standard high rise or stuff like that. So I guess based on after working in all these industries for different companies, what made you want to go the consulting route and how are you enjoying consulting?
Terry Dussault:
Yeah, so that’s a good question. I think for me, I got to a point in my career where I had a business way early on. When I was 19 years old, I started my first business. So I’ve always had an entrepreneurial spirit at heart and I’ve went to work for some bigger companies and things and I learned a lot. So I have no regrets about that. But I got to the point with my knowledge of construction, with my knowledge of environmental and then the safety side of things, the requirements, whether they’re regulatory requirements or company policy type requirements that I felt like I could offer companies a lot of guidance on how to navigate safety at their companies. So that would be like if you’re a business owner or maybe even a well established business of 300 employees and maybe that company is trying to improve their competitive performance and reduce the amount of incidents that they’re having. I felt like I have enough experience to dive into consulting.
Steven Rossi-Zalmons:
Yeah, that’s good to hear. I’m sure starting any business, but especially something like this that’s generally pretty reliant on being in person must’ve been a challenge during that time. So just to dive into some more specifics in terms of safety and specifically workplace safety and safety on construction sites, can you tell us the importance of having an effective safety plan?
Terry Dussault:
Yeah, it is very important and on a lot of levels, and I’ll try and go through them as best I can here, but as employers, we’re obligated to make sure that we identify all the potential hazards that are in a workplace and communicate those hazards effectively to workers. Okay, so let’s say for example, we work in a static, what I’ll call a static work environment, which means we’re in manufacturing and every day we’re making widgets. Okay. The importance of having a safety plan is to make sure that you’re covering everything as far as what the physical hazards may be in that workspace. So let’s say you’re running blades or you’re running drill presses and those types of manufacturing equipment or in your processes, maybe you’re doing platting type of stuff for metal or coatings and things like that. There’s chemical hazards. So the idea of having a safety plan is to make sure that you have something that’s formal and written that identifies those physical hazards and the chemical hazards and just an overall plan for what you’re going to do in the event of an emergency.
And a lot of times in those environments, the manufacturing environments, lockout-tagout is a big concern when you’re working on energized equipment. And so you want to make sure that the safety plan addresses all those types of things, the high risk work or what I would call the permit work. So if you have a facility that has a 30 foot roof on top or up on the roof you have access to that roof, how do you prevent employees from climbing the ladder on the side of the building and going up on the roof? Who’s allowed to go up there? What precautions or safeguards are in place to make sure unauthorized people are not allowed to go up there because there’s the potential somebody could fall off, fall through a skylight, things of that nature. In California here where I’m at, we have a lot of skylights.
So anytime somebody’s working at heights, that’s high risk work. And so it’s just important overall to make sure that the facility has a safety plan. And then on construction sites, it’s even more important because that’s not a static environment. That’s what I would call a dynamic environment. So I’ve written about 600 safety plans for clients that do construction and environmental work. And what I’ll usually do is start by reading their scope of work. So I asked for the contract documents because what I want to make sure of is that every aspect of the safety plan that we produce is adequate enough to communicate all the hazards to the employee because it’s kind of like a legal document in a way. So if I send you out to a site and I don’t identify that there’s chromium-6 in the soil from a former platting operation, and then somebody else tells you to go, “Hey, Steven, we need you to go take that shovel and go start digging over there.
We need to dig a trench.” And now you’re in the middle of a area that’s contaminated and even though you can’t see the hazards or you don’t know that you’re being exposed, that’s a super toxic chemical. And so I deal with a lot of that kind stuff, the hazards that you really can’t see that are super dangerous. So it could even be a confined space on some of the industrial projects I’ve done work on. I remember I had this one, it was a former refinery, but it was a privately owned refinery, and the people in that community wanted to get rid of the refinery. They didn’t like it. The community grew around it and it was outdated and such, and we had to put workers inside a giant tank. It was like a slop tank that had a lot of chemicals that were unknown.
And so we had to figure out a way to get the chemicals out, solidify the liquid sludge and be able to put workers in there to do what they needed to do without them dying essentially because it’s a confined space with unknown chemicals. So we had to use breathing air and have all kinds of rescue plans and backup systems just to make sure if something went haywire, they had backup, breathing air alarm systems so that we knew some because you couldn’t really see very well in these tanks and things like that. So yeah, you got to really look at each job and try and pinpoint what those hazards are and how you’re going to deal with them. So yeah, the safety plan is the heart and soul of how you’re going to do that work safely. So it’s really important.
Steven Rossi-Zalmons:
Yeah, absolutely. Yeah, that’s interesting. I’m sure you must have a range of stories that’s really interesting one from different projects, and it’s good that there’s people like you thinking about the things that we can’t see that can and protecting us from those. So I guess part of the safety plan and is also incident response, so can you tell me what the five essential steps of an incident response plan are?
Terry Dussault:
I’m glad you’re bringing this up because I also do a lot of incident investigations. I’ve done hundreds of them. Some of them for people that just pinch their finger all the way to losing a finger, some other serious ones where people have fallen off roofs and gotten hurt pretty bad. So the reason I think it’s important that you’re asking this is because preparation I think would be step number one, which isn’t really an essential step of the response part, but it’s important for people to know that your preparation is really key and preparation, what I’m talking about specifically is training, making sure people are trained and doing drills to make sure that everybody really knows what to do if something does happen, having a person that’s designated as a safety officer that’s leading the incident investigation or the response or whatever, and not everybody can size up the situation when an incident happens.
You need somebody that could really size up the situation and figure out what to do. So it starts with also identifying what type of an incident you’re dealing with. Is it a bodily injury? Is it a property damage incident or even a security incident? At work you could have some kind of a security incident like workplace violence or even some kind of harassment, which these are big things that are hot buttons right now in the workplace, like making sure people have their workplace violence training and sexual harassment training and all that, because sometimes the small harassment things, they don’t seem like much, but then it builds over time and management has no idea the stuff’s going on and next thing you know it you have a situation.
So identifying what type of incident you’re dealing with is really important. After that, I would say getting help because being able to obtain help and then provide first aid if you’re a first aid CPR certified person, and as far as getting help and sizing up the situation and all those things that I’m telling you, it’s important for people and employers to know who they’re putting in these positions because there’s been incidents that I’ve investigated where the person that you think will be the most reliable in a crisis will fall apart. Sometimes they don’t like the sight of blood or they panic, people just panic.
And I remember I was doing a safety training one time with a guy. It was a group, but this particular construction worker told me that he fell on a piece of rebar, and I think it was like in the morning time, and he said he was standing next to a trench. He was the first one on site. He had went down in this trench and tied a piece of rebar horizontally because there was a lot of vertical pieces. So it left some vertical rebar about maybe 10 or 12 inches high. His boss shows up, they start talking, he jumps out of the trench, they start talking about what they’re going to do that day. And as they’re standing there next to the trench, he lost his footing because the sidewall of the trench collapsed and he fell in and he fell on the rebar and it went up inside him about 10 or 12 inches.
And his boss panicked, didn’t help him. The guy ran to his truck, got in it and left, and left him on the rebar. And he told me, he said, “Terry,” he goes, “that incident took two years off of my life.” He somehow was able to get himself off of the rebar, climbed out of the trench, got in his truck. He was in total shock and drives himself 20 miles to his house. And when he walked in the front door, he said he collapsed at the front door, but he needed multiple surgeries and all this kind of thing. And I’ve heard this happen many times now because I’ve been doing this long enough where it’s important to know who you have in those places that are going to be responsible for safety because you just don’t know how people are going to respond to a serious incident.
And that might even be a workplace violence situation or everybody’s different. You can’t gauge how I’m going to respond, even if you’ve known me 20 years. I could just cave in and not really be able to help much. Especially you don’t know that side of me. So sometimes people end up in these positions and you go, “Well, why was that person in that position in the first place if they couldn’t handle it?” Nobody knew. There’s no real true test for that. So I would say make sure the next thing, because you said five, securing the scene is important. Once you get help, make sure help’s on its way. If you can’t administer help or get that person off offsite or to a facility somewhere, making sure that the scene is secure is the next important step. And then communicating the incident to the stakeholders or people where that information it needs to be routed to.
So that could be a boss, it could be a number of different people, and that really depends. Communication is really important. Making sure all the key people know something happened. And sometimes if it’s a spill, that’s super important too because like a drum of contaminated groundwater or a material that spills into a storm drain or some kind of a sensitive receptor, the regulatory agencies have strict guidelines about reporting. And this again, is another reason why you kind of… It’s important to have a site specific safety plan when you’re out on projects because it’ll identify all this in a perfect world. But then the follow-up really is to investigate the accident or the incident and see why did it happen, what were the root causes, and then figure out is there a way that there can be an improvement made so that it doesn’t happen again. So we would call that the solutions.
And investigating accidents is also great because you can share the lessons learned with your organization. So instead of let’s say hiding it, let’s say we’re managers and we don’t really want anybody to know, it’s not serving the company very well because it’s always better to be transparent. And that way you can learn and teach people like, hey, look, this happened. And then sometimes if you have a really good safety program, you start to see a lot of reporting and not just for the incidents but near misses, and you can share those learnings and you see trends, you start to see trends come up. So it’s kind of important. But that’s pretty much it. Developing the solutions is important at the very end because a lot of companies don’t do that, so they keep having incidents happen, but they’re not really… They don’t have time to do an incident investigation. They don’t want to do it, or they just don’t see the value in it. There’s a lot of value in it though.
Steven Rossi-Zalmons:
Yeah, absolutely. Yeah, that’s definitely the most important part if you’re not learning from your mistakes, then you’re just going to keep repeating them. So you’ve touched on so many different types of incidents. It’s really expanding what I was even considering as workplace safety, but it makes sense. It’s more than just physical, and each one is equally important and equally serious. And it’s important to have not just one person, but multiple people ready to help in case things happen and people are unable or in shock, and then be able to deal with the situation.
Terry Dussault:
Yeah, I think having some backup, it’s just good to really know your team, and some people are really good under pressure. They just know exactly what to do. And then other people not so much, but you know your team and you can really start to build your safety program around your team too. And mentoring others is important.
Steven Rossi-Zalmons:
Yeah, for sure. Going back to construction specific, you touched on this a little bit before of how construction sites are very dynamic. On construction sites specifically you’ve mentioned there’s lots of moving heavy equipment, moving pieces, numerous hazards, both static and dynamic. What would you say are the best strategies that construction companies can implement to prevent incidents on their sites?
Terry Dussault:
Well, I think training is always key. And the one thing that gets missed a lot I think is onboarding training. And when you start bringing in people, and building your business or your company, making sure that those people in the field that are going in the field understand how to identify hazards properly. That would be number one. And also providing them the training for how to do that, because it’s easy to assume people know that already or like, oh, that should be common sense, but not so much. That’s not really how it is. So you have to take the time to train them, make sure that they’re mentored. Or in a lot of cases, like working with the oil companies, they have a program, it’s called the Short Service Worker Program.
For the first six months, the person is supposed to be mentored, and they actually will even give them a different colored hard hat so that everybody knows the person with the green hard hat is new to the company. So they might have experience still, like they’ve worked in a similar industry, but when they all have the green hard hats, you know they’re new to that company. And so it makes it really easy if you’ve got a hundred workers and you’ve got 20 with green hardhats, you know you have a lot of short service workers, and those are the ones that might be at the highest risk so you really want to pay attention to those workers. That’s one thing.
And then as far as identifying hazards, it seems like it would be easy, but I’ve kind of developed a system over the years and I’ve realized, okay, there’s 10 different hazard classes, and I came up with the system for how to remember that, and I’m not going to get into all of that, but once you memorize it, and then we also have this form we use, we call it a hazard hunt, and we came up with this system and when we implemented it, people, a lot of the workers were like, really, Terry, we got to do this. You want us to go walk around the site, identify hazards, and just use the form and do it and make it fun and see what you can find and come back. So we try to make it fun and there’s different incentives and things you can do for that. After we started doing that for a while, some of the workers came back and they said, “I can’t believe how that changed my thought process on hazards now.
Now when I see something, in my head I’m trying to categorize it and put it in one of the categories that you told us about or you taught us.” Really, it’s kind of a good system, but a lot of workers are not formally taught. It doesn’t matter if you’re in construction or you’re a truck driver or you work at a pizza place down the street. The hazards are generally the same in every industry. Once you learn the 10 different hazard classes, it makes it easy to identify the hazards. Once you know how to do that, it makes it easier to learn how to mitigate the hazards and not get yourself in a position where you’re standing behind a piece of a heavy equipment or in the swing radius of a piece of equipment because you’ve learned about impact hazards. It’s a lot, it sounds like a lot, but it’s really not when you break it down, but it just taking that time to teach people how to identify the hazards. There’s a lot of ways to do it.
Steven Rossi-Zalmons:
Yeah, having workers being able to identify them is definitely important. So, yeah, otherwise they’re the ones who are at risk. It’s good that they can identify and prevent them as well. So you’ve been in workplace safety for a long time in different industries. How have you seen things evolve in terms of workplace safety and have you seen things evolve and have things gotten better throughout your time or what changes have you seen?
Terry Dussault:
Oh yeah, I think I’ve seen a lot of change. In fact, when I first started doing work with the oil companies, one of the things I did is I worked on their retail petroleum sites where they had the filling stations and we could show up on a job site with just a baseball hat and work boots. It was like, oh, this is great, except when you’re out on one of those sites and they have a lot of traffic. You’re out there like a regular person and the cars are everywhere. So then they came out with high visibility vests and the requirement for that, then it was gloves, then it was something else, and eye protection and so on and so forth. And a lot of times when these changes were implemented, it came because there’s a price. So the oil companies want to make sure that they don’t have a lot of incidents on their projects.
So yes, I’ve seen a lot of changes with PPE itself. One of the coolest things to look out for if you’re not aware, is there’s a huge change right now that’s occurring with hard hats because the conventional hard hats, as we know them today, the design on them hasn’t changed since the 30s. And the testing of how they actually test a hard hat in a lab, that testing requirement or standard hasn’t changed either. So what they have learned is that there’s a lot of traumatic brain injuries when people are struck on the head from the side, regardless of whether you have a hard hat on or not. And hard hats are tested from the top down when they do the test in the lab. So there’s these helmets now that people are starting to wear and some of the oil companies are requiring, they are more safe for side impact type of incidents that occur and preventing traumatic brain injuries.
There’s a whole study on it I won’t get into, but you have that as far as advancements. And then the advancements that I’m excited to see are the stuff that you see in heavy equipment. It’s like your car, a backup camera and things like that. They have some pretty high-tech stuff that’s going in heavy equipment, not only for safety, but also just for being able to operate the machine more effectively. So they can do surgical excavations. Basically they don’t even need an operator. The machine will drive itself. So that’s exciting to see I think. For safety one of the things I do as well is I do a lot of site inspections, and last, or this year I’ve done about 160 job site inspections for a variety of companies. And when I go there, I typically am on a job site for an hour or two, and then I do a report. But there’s a lot of technology now around cameras that can scan the work site and it can scan and watch more than one worker at a time.
And it can tell you if they’re wearing gloves, if they’re wearing safety glasses or not, and it can record it all on a spreadsheet kind of thing, and it’ll give you a better picture of how well safety is being adhered to as opposed to a guy like me, I’m coming out to the site and I’m doing my observation, but it’s not as thorough as the technology is. It’d be kind of cool to be on the front end of it and go buy some robots and put the robots out on the job sites, what it’s going to come to. But I thought, well, that would be great, and it would be an interesting test to jump in on that, but it might start freaking the workers out because they’ve got robots monitoring. So I thought, well, how could I get around that? So I thought, well, maybe I’ll just dress the robot up like Chewbacca. Everybody likes Chewbacca, so you got to be creative. I’ll probably get sued by George Lucas if I do that so I don’t know if that’s really going to happen.
Steven Rossi-Zalmons:
Yeah, you might have a licensing issue there.
Terry Dussault:
Yeah.
Steven Rossi-Zalmons:
But, yeah, no, that’s a good point. And yeah, that’s interesting that there’s so much new tech and yeah, I’ve definitely seen, and we’ve spoken to companies who are involved in some of that, both in terms of worker safety and also automating tasks and doing different things to make just tasks safer or to entirely remove the operator from the danger so they can operate things remotely. Yeah, it’s great to see all the new technology in both software and hardware that’s coming out to help with this.
Terry Dussault:
Yeah, I’d love to hear more about that and know what you’ve come across and what you’ve heard about it because it’s interesting to me. A lot of people are afraid of advancements and all this technology and everything, but I kind of embrace it. I like it. So to me I think it’s whatever we can do to improve is positive as long as everybody’s on board.
Steven Rossi-Zalmons:
Yeah, for sure. I mean, I think the construction industry is generally pretty slow to adopt these things, but the innovations are there and it’s about people like you and in the industry accepting and driving them forward so that we can use them and make it a safer place for everyone and more efficient as well.
Terry Dussault:
Yeah, yeah. I got a good story for you that’s kind of related to tech that I’ll share with you. This happened probably 15 years ago, but I was doing some environmental work at, it’s a fueling terminal here in Los Angeles and in this fueling terminal, it’s one of the biggest ones in the LA Basin, and they have about 20 big rigs that are coming in one after the other. Not when I say 20 big rigs, I mean they have 20 slots. So these big trucks come in, the fueling trucks and the trucks are lined up like five deep. And so when they come in and they fill them from the terminal, it’s like they call it the rack. And the rack is where they all pull in and the rack is because if there’s any kind of a fire, it could really cause a huge problem.
They have tanks with a million gallons of fuel in them and that they’re above ground, and it would be terrible if there was ever a fire there. So they have these sensors that they put in and it’s like an eyeball, and they put them pretty far away from the rack, but the whole rack is being observed by these sensors and they don’t really allow welding on the site. And so one day they had to do some welding and they had a subcontractor out there and they used these shields, and so all the welding has to take place within this little area that’s been shielded. But the shields didn’t go all the way to the ground. And so the eyeball or the sensor saw a flame, and when it saw the flame from the welder, it triggered an alarm and the whole rack with 20 big rigs was immediately submerged in foam.
They have these giant units. I never even knew this could occur. It was never told to me. I never saw it myself, but one of the guys that I worked with saw it and he said, Terry, this was the craziest thing. He said within three seconds, that whole rack looked like it was under foam, and all of a sudden you just see guys, all the truck drivers running out and they looked like marshmallow men. They had foam all over them, but it took… What’d they tell me? It took like eight hours to recharge it with foam and clean up all the mess. And the impact of that, just that incident was so significant that it changed the price of fuel in the LA Basin because everybody, it stopped getting their fuel so it had an impact. But it’s crazy. But that’s all you know… And that’s old tech stuff. That’s not even the new stuff. So a lot of the new stuff, it’ll be really interesting to see how it all works out.
Steven Rossi-Zalmons:
Yeah, if it’s a lot of foam I’m surprised it only took eight hours, honestly, to clean up that much. But yeah, that’s cool. All right, well Terry, thank you very much for joining and for sharing all your different stories you have. I’m sure there’s many more that you could share.
Terry Dussault:
Yeah, probably.
Steven Rossi-Zalmons:
But we’ll save that for another time. So thanks again for joining us. Have a great day.
Terry Dussault:
Yeah, thanks Steven. I appreciate it. Take care.
Other Related Episodes
Episode 54 |
February 6, 2025
Smarter Water Management for Safer and Greener Construction
In this episode of The Construction Revolution Podcast, Steven Rossi sits down with Yaron Dycian, Chief Product and Strategy Officer of WINT Water Intelligence. With over 25 years of experience driving strategy and innovation at leading companies like IBM and RSA, Yaron is leading the charge in AI-powered water management solutions. Tune in as Yaron shares the story of WINT, explores the rising challenges of water damage claims, and discusses how advanced monitoring and leak mitigation technologies are shaping the future of construction. From preventing costly damages to meeting sustainability standards and lowering carbon footprints, this episode offers valuable insights into how construction companies can stay ahead in a rapidly evolving industry.
PLAY
Episode 52 |
November 14, 2024
Advancements in Low-Carbon Construction Technologies
Join us for an engaging and insightful panel discussion from 2024 Net Zero Construction Conference, hosted by Aali Alizadeh, Ph.D., Co-Founder and CTO of Giatec and Technology Chair of The Net Zero Construction Conference. This episode dives into groundbreaking advancements in low-carbon construction technologies, highlighting both the promising opportunities and the significant challenges involved in their industry adoption.
Our distinguished panel of experts features: Professor Jason Weiss from Oregon State University, Heather Brown, Ph.D., Vice President of Quality Control/Quality Assurance at Irving Materials Inc. (IMI), Donn Thompson, Senior Director of Building Innovations at the National Ready Mixed Concrete Association (NRMCA), Brandon Williams, Business Development Manager at Sublime Systems, Lisa Barnard, Sustainability & EPD Program Manager at Chryso Saint-Gobain, and Pouria Ghods, Ph.D., Co-Founder and CEO of Giatec. Together, they offer a wealth of knowledge on the latest advancements in sustainable construction, sharing how innovative materials and solutions are transforming the industry.
Don’t miss this opportunity to learn from industry leaders as they share actionable insights and strategies that can drive meaningful change in the construction landscape.
Want to dive deeper into conversations like the ones in this episode? Join us at the Net Zero Construction Conference 2025 on March 19-20 in the Virbela Metaverse! Experience two days of expert panels, innovative insights, and networking opportunities focused on low-carbon construction technologies. Learn more and get your tickets on the N0CC website!
PLAY
Episode 51 |
October 24, 2024
Maximizing Profit Margins for Construction Businesses
In this episode of The Construction Revolution Podcast, Steven Rossi sits down with Elizaveta Taylor, founder of Beyond Books Solutions. With extensive experience in construction accounting and advisory services, Elizaveta is dedicated to helping construction business owners save time, money, and increase their profits. Tune in as Elizaveta discusses the common financial challenges faced by construction companies, shares strategies for maximizing profit margins, and offers expert advice on cash flow management. From overcoming money mindset blocks to optimizing QuickBooks for construction businesses, this episode is packed with valuable insights for anyone looking to improve the financial health of their construction business.
PLAY
Want to Be a Guest Speaker, Sponsor, or Just Have a Question for Us? Fill In the Form!