Take Thermal Control of Your Concrete with SmartRock
Mass concrete pours are becoming more and more present in the construction industry. As our ambition grows, the size of our concrete structures grow with it.
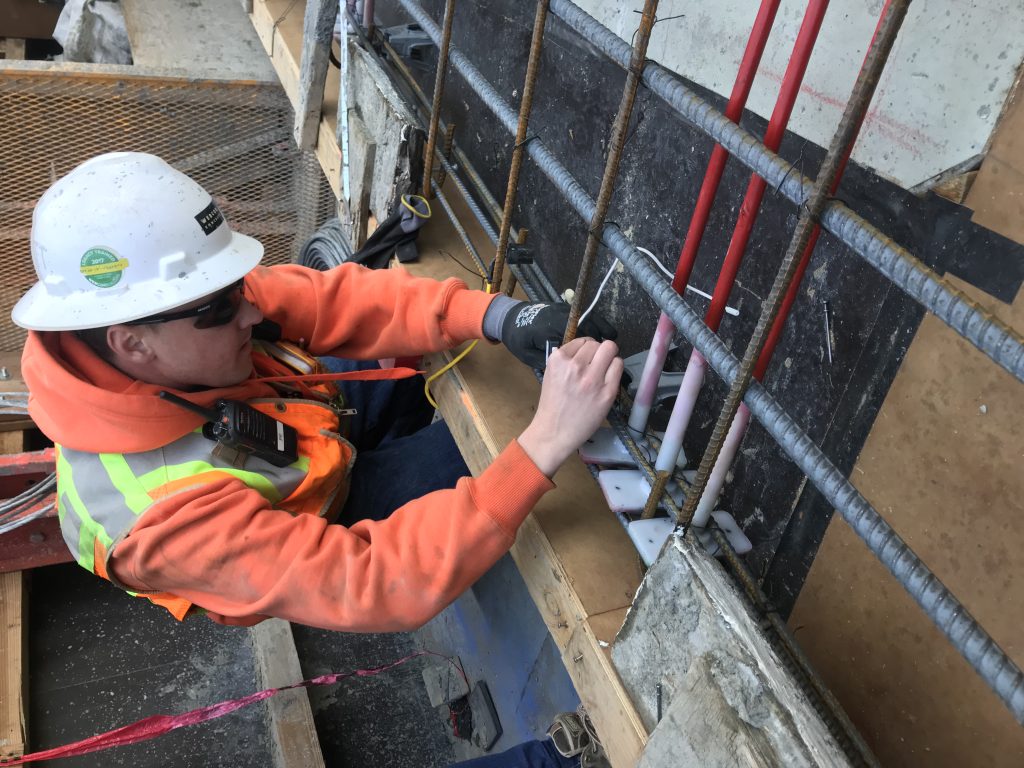
Mass concrete pours are becoming more and more present in the construction industry. As our ambition grows, the size of our concrete structures grow with it.
Mass concrete pours are becoming more and more present in the construction industry. As our ambition grows, the size of our concrete structures grow with it. Massive pours have their specific set of challenges that must be anticipated and prepared for, including the thermal cracking of structures. In a fresh concrete element, the center will retain the heat generated by the hydration of the cement, whereas the surface will be cooled down by the ambient temperature. This creates unequal expansion and contraction, which can lead to cracking in massive pours if the thermal strain is higher than the tensile strength of the concrete. Even though mass concrete pour conditions are not ideal, they are manageable with a properly executed concrete thermal control plan and the efficiency of wireless concrete temperature sensors. We will get into all the details soon. But first, let’s find out what exactly thermal control plans are and when they are used.
Want more information on the temperature gradient and thermal cracking? Click here!
In short, a thermal control plan allows contractors to monitor the temperature of early-age concrete in order to ensure that the maximal temperature gradient is not reached so that it cures properly. These temperature monitoring procedures are specific to the project and concrete mix being used. They define the concrete temperature limits as well as the maximum concrete temperature differential between the core and surface in order to prevent concrete cracking and other quality issues. They also state how often concrete temperature should be measured. Many engineers, contractors, DOTs, and other specifiers require the use of thermal control plans, especially during:
The typical concrete thermal control plan will provide specific instructions to account for the predicted heat generation. Logically, the first step is to determine the temperature increase coming from the selected concrete mixture. There are different ways to achieve this approximation, but the simplest is to base the heat generation on the cement content of the mix. ACI 211.1 “Standard Practice for Selecting Proportions for Normal, Heavyweight, and Mass Concrete” suggest a temperature rise of 10 to 15 °F (5.5 to 8.5 °C) for every 100 lbs of cement per cubic yard of concrete (59 kg/m3). This method of calculation only gives a general idea of the heat generated, as other components of the concrete will also have an impact on the final result. Based on the approximation, it is determined whether the mix design chosen is appropriate for the job.
Then, the concrete supplier must be alerted and informed of the fact that the mix is for a mass pour or extreme weather. The maximum temperature of the concrete at placement must be provided to the supplier to assure that the concrete will be at a good temperature after the pour (not too high). On their side, they can use cold water for the mix or cool down aggregates before mixing using cold water. There are many possibilities to reduce the initial temperature of the concrete.
Then, the last major part concerns the measures taken by the contractor to reduce the heat rise in the concrete. Those measures are based on the many temperature limitations in concrete:
With this information and the heat rise prediction from the concrete mix design, the applied measures can be developed for specific jobsites. Onsite, the most used method is to isolate/heat the surface of the concrete at the desired temperature. This can be done by creating a heated chamber around the element and heating that chamber. In some other cases, a core cooling installation can be prepared before the pour. This is usually made of a pipe system that can pass water through the core of the element to reduce its temperature when necessary. This method is usually used in even bigger pours where these additional measures must be taken.
The next logical question is how the efforts applied to control temperature onsite are measured. The type of action and their regularity will be defined in the thermal control plan. With these measures, it will be known if the efforts are effective and if the concrete stays within the limit set in the plan. This is how you can control and ensure that you’ve met all the requirements in your thermal control plan.
For decades, contractors and project managers have relied on wired systems like thermocouples and data loggers for concrete temperature testing. Not only are these traditional methods expensive, labor-intensive, and time consuming, but they are also proving to be less accurate than today’s concrete sensors. If not assembled or labelled with care, thermocouple wires can get tangled,resulting in errors during data collection.
Learn more about testing equipment for concrete thermal control plans here!
SmartRock® wireless concrete temperature sensors are quickly becoming the new standard at construction jobsites all over the world. The speed and accuracy of these award-winning concrete sensors are cutting weeks off project schedules by sending real-time concrete temperature data directly to contractors’ mobile phones. This eliminates hours of manual work gathering data from thermocouples while reducing the risk of human-error. TIC used SmartRock to finish 1.5 weeks ahead of schedule!
Here are a few more reasons why contractors in over 80 countries now choose SmartRock:
Wish you didn’t have to be at the job site to access your concrete temperature data? With Giatec’s SmartHub™ remote monitoring system, you don’t have to be. You can access concrete temperature data recorded by your SmartRock sensors from anywhere, at anytime. How does it work? SmartHub collects the sensor data and sends it to the cloud. The data is now safely stored in the cloud and available for you to view from your desktop, laptop, or mobile device. You can even set up alerts that tell you when your concrete has reached the temperature gradients specified in your thermal control plan.
No matter what kind of project you’re working on, you can achieve great results and ensure quality with a thermal control plan. If properly developed and executed, thermal control plans will stop concrete cracking and shrinkage, ensure adequate concrete strength gain, and prevent other quality-related issues with your concrete. To get the most accurate concrete temperature readings in the fastest possible time, use SmartRock wireless concrete sensors. Take control of your concrete, avoid thermal cracking, achieve huge cost-savings, and move your projects along faster!
Étienne Noël is a Co-op Lab Assistant at Giatec’s Research and Development Department. He is currently a 3rd year student at the University of Ottawa pursuing a Bachelor’s in Civil Engineering. Working in the Research and Development department for Giatec has allowed him to greatly deepen his knowledge of the concrete industry. Giatec’s non-destructive approach to revolutionizing concrete testing is a topic that quickly interested Étienne and which he now wishes to share in order to advance in an intelligent concrete industry.
Étienne Noël is a Co-op Lab Assistant at Giatec’s Research and Development Department. He is currently a 3rd year student at the University of Ottawa pursuing a Bachelor’s in Civil Engineering. Working in the Research and Development department for Giatec has allowed him to greatly deepen his knowledge of the concrete industry. Giatec’s non-destructive approach to revolutionizing concrete testing is a topic that quickly interested Étienne and which he now wishes to share in order to advance in an intelligent concrete industry.
*Limited kits available. Claim yours today!